"Our future killer technology for creating the part that allows customers
to say they will buy these products because they are our products is ICT
(information and communications technologies)".
It is more than 120 years since it was founded as a shipyard (about 140
years since its foundation of business). Kawasaki Heavy Industries, Ltd.
(Kawasaki) has been not only accumulating advanced technologies and know-how
for manufacturing as a comprehensive heavy-industry manufacturer but also
expanding its business areas steadily. One of 6 Companies that constitutes
Kawasaki today, "Energy System & Plant Engineering Company"
has "Marine Machinery System Division", which is responsible
for marine-related machinery. In "Systems Engineering Department",
in the Division, which deals with propulsion system products that integrate
the engine and propeller, communications technologies and software are
regarded as very important element technologies. For this reason, Mr. Takenori
Hino, Senior Manager of the Dept. draws strategy that Systems Engineering
Department is willing to take the leadership by themselves.
Our user to pick up for this issue is "Systems Engineering Department,
Marine Machinery System Division, Energy System & Plant Engineering
Company", which deals with advanced propulsion systems to mount on
ships, in Kawasaki Heavy Industries, Ltd. that holds a wild range of business
divisions.
The Dept. has been exploring evaluation and verification of performance regarding DPS (Dynamic Positioning System: automatic fixed-point-hold function) or hybrid propulsion systems, which are attracting attention in the area of propulsion system products, or possibilities of utilizing technologies for visualization and simulation that support experiences of operationality. At the end of 2016, they started developing a simulator for experiencing steerage of the hybrid propulsion system virtually by linking the simulation model (a ship behavior model) that they had been developing on their own with the real time 3D VR of FORUM8 "UC-win/Road". The simple early version of this was produced in Feb. 2017. Since then, improvement was made step by step through collaboration of both. In the spring of 2018, the present version of simulator was developed, which reflects motion of the operator.
Founded as a Shipyard More Than 120 Years Ago, Kawasaki Keeps Expanding Its Foot and Globalization
In 1896, Kawasaki Heavy Industries, Ltd. was founded as Kawasaki Dockyard
Co., Ltd. in Kobe. Its origin dates back to 1878, 18 years before the foundation
and about 140 years ago, when Kawasaki Tsukiji Shipyard was established
in Tsukiji, Tokyo.
Later, as it expanded its business from manufacturing ships and vessels to steam locomotives, aircrafts, bridges, and automobiles, the Shipyard made its organization partially independent or reorganized step by step. In 1939, it changed its name to the current name reflecting its business categories.
While expanding its business affairs also after the World War II, it promoted split-off of operational departments and merger of group companies. In such a process, the Company has repeated bold reorganization and marketing, reflecting social environment or the demand of the age. For example, an in-house company system was introduced in 2001.
Kawasaki currently holds nearly 36,000 employees at its domestic and overseas business and manufacturing bases including 2 headquarters in Tokyo and Kobe and 93 consolidated subsidiaries. Consolidated sales amounts to over 1.5 trillion Yen (figures as of March 2018).
The in-house companies that drives Kawasaki's business consists of 6 organizations
including Ship & Offshore Structure Company, Rolling Stock Company,
Aerospace Systems Company, Energy System & Plant Engineering Company,
Motorcycle & Engine Company, and Precision Machinery & Robot Company.
Among them, Energy System & Plant Engineering Company conducts global
business on various industrial machinery including a wide range of industrial
plants, facilities for energy and environmental conservation, turbines
and engines for marine and land.
Committed to Disseminate Advanced Propulsion System Products
"Systems Engineering Dept., Marine Machinery System Division", the focus for this interview specializes in marine machinery out of a wide operation area of Energy System & Plant Engineering Company. The Dept. deals with 2 product fields broadly: propulsion machinery products to load on ships such as marine engines and propellers for ship propulsion, and propulsion system products such as DPS and hybrid propulsion systems. They work on electric control of individual devices and creation of new values through integration and systematization of these devices.
"Even if each propeller, engine, or a generator is operated optimally,
it is basically unknown if it (the aggregate of optimal devices) is actually
optimal (functions as an optimal system) when considered as a whole ship."
Yoshiteru Harada, Manager, Integrate Systems Engineering Section says that
the role of their Section (of Integrate Systems Engineering) is to build
up a system from the view point of "how to create an optimal whole
by combining individual devices" from the beginning,
One of the propulsion system products that the Dept. pays particular attention to, DPS is a technology of steerage to hold the position and orientation of the body of a ship automatically (automatic ship steering). As a specific scene of applying it, Mr. Hino, Senior Manager mentions marine construction to construct various kinds of structures such as facilities for excavating resources or wind turbines using cranes etc. loaded on a ship while holding the position and orientation of the ship by DPS (the fixed-point holding function). In addition, there are abundant use records as a function for supporting berthing/leaving to surely control the position and orientation in berthing/leaving of ship. Moreover, Kawasaki Integrated Control System (KICS) is a system that integrates ship steering elements such as controllable pitch propellers, azimuth thrusters, side thrusters, and rudders. This enables DPS and route tracking to automatically navigate on a charted course, by operating it with the joystick and heading control dial and interlocking it with different navigational devices. According to him, it brings out the capacity of the ship as much as possible since it automatically determines the optimum blade angle, rudder angle, and speed of rotation depending on the ship steering mode. It also allows labor savings.
|
|
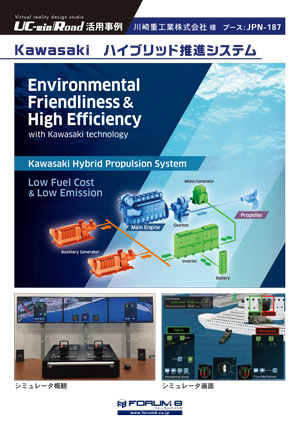 |
Poster explaining Hybrid Propulsion System |
|
Another main product of propulsion system is a hybrid propulsion system.
"There are two necessary kinds of energy for ships: energy for propelling
a ship, and energy for people's living in the ship or operating devices
loaded in the ship."
Previously, each one was equipped with independent generator and engine to supply energy. The task was how to reduce environmental load and improvement in fuel efficiency. Then Kawasaki develop a way to control generally by combining engines, generators, motors and propellers etc. Mr. Hino explains that they have been developing a hybrid propulsion system for minimizing (optimizing) the energy consumption for the whole ship by exchanging energy mutually. |
Constructing Simulator for Hybrid Propulsion System Step by Step
At the end of 2016, Kawasaki was preparing for International maritime exhibition and conference "NOR-Shipping 2017 (Norway)" to be held in May in the following year. Mr. Hino and others were examining how to present their hybrid propulsion system to users.
It was when "we were beginning to demonstrate our hybrid propulsion system in the (domestic and foreign) market". There was limitation on explanation using only paper leaflet as before. It was rather hard to allow customers who conduct ship operation to understand its effect, which was important to them. They thought that after all it would be effective to have visitors to actually operate the simulator to feel the bodily sensation of the effect of the system. Additionally, such a simulator was considered useful in examining or verifying the system in advance in the developing process within the company. Therefore, they focused on utilizing "UC-win/Road", which has abundant records in driving simulators (DS) in the automobile field as well as flexibly supports needs for customization in the design of VR or CG. In their conception, it was planned to build up environment where users steer ships and ships move based on signals of control devices in VR space by linking Kawasaki’s control device with UC-win/Road and using levers and controllers in the end.
However, as it is difficult to reach this level suddenly, they incorporated the simple simulation model of ship behavior that Mr. Hino and others had been developing into UC-win/Road, and created VR that represented ship steering image with the hybrid propulsion system along the scenario in Feb. 2017 as the first step.
They exhibited it at "NOR-Shipping 2017 (Norway)", which was an opportunity to start a series of efforts. Mr. Hino reviews that visitors realistically felt the effect of rich presence brought about by this new way of explanation.
While improving the functions of the simulation system of the early stage gradually, they showed it in the exhibition held in Holland in the same year. Later, they upgraded it to the current system, which is set up so that the ship in VR moves reflecting the operation of simulator, as the second step.
The new simulator has been shown in the International maritime exhibition and conference in China held at the end of 2017, followed by those in Japan, Singapore, Holland, and Germany in 2018, while providing improvement and additional functions at any time.
|
|
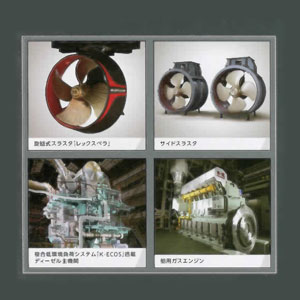
|
Products using Marine Machinery System |
|
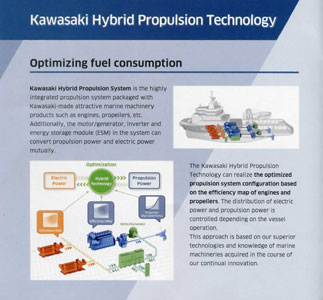 |
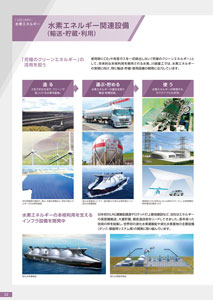 |
Hybrid Propulsiion System |
|
Further Improvement in Reality and Support for Autonomous Ship Planned
"Our image of goal is to make the presence felt as Kawasaki Heavy
Industries by working to realize 'Autonomous ship', which matches autonomous
vehicle driving."
The key to this is ICT, as mentioned at the beginning. Mr. Hino says that it includes not only the technologies mounted on their products themselves but also simulation technologies that allow visualization of system performance and evaluation/verification in advance.
In this sense, they highly evaluate the effects of simulation they have built up through collaboration with FORUM8 for more than 2 years and its flexible response to user needs. On the other hand, in order to advance the reality of simulation more, they analyze that they need to clear their problems such as improving the system by adding immersive feeling or creating stricter mathematical models regarding ship behavior.
Furthermore, Mr. Harada pays attention to the significance of collaboration between KAWASAKI and FORUM8 in each of their areas of expertise for the two elements that are important for enhancing reality (technologies for visualization and simulation). He told that there was some impressive exchange between them. In particular, for example, they received a positive proposal from FORUM8 about representation of waves based on minute research.
Mr. Hino thinks that an autonomous ship is a system that contains more complex and wide range of elements, and that it will be harder work to develop simulation technologies for this.
"For this to realize, I think visualization will be an essential technology.
I expect further cooperation of FORUM8."
|