On the other hand, DENSO has business units to deal with individual product areas, and several business groups, each of which comprises 3 or 4 business units by category. One of them is the Information & Safety Systems Business Group. Aiming at realization of highly qualified mobility society without traffic accidents, the Group targets development of technologies for ensuring confidence and safety including automated driving technology.
Positioned as a semi-business unit that forms the above Business Group, Electronic Control Components Division takes charge of technological development on electric and electronic products that compose EPS. Within the Division are Departments specializing in particular roles by function. Among them, Electric Control Engineering Planning Department, of which Director is Mr. Nakane, not only performs product development of the concerned area but also examines business strategy in consideration of the future technological trend.
|
In contrast, Electric Control Engineering Department performs detailed designing for mass-production of the developed products etc. This time, Mr. Kazumi Arimoto, Manager of Technology Section 4, Electric Control Engineering Department took charge of constructing a simulator for feeling bodily sensations of 2-Drive EPS. Section 4 assessed the developed products from various angles through diverse
EMC tests and environmental tests, as a preceding step before mass-producing
them. In addition, Mr. Hideki Amakusa, Project Assistant Manager who took
part in developing the scenario and simulator using UC-win/Road, is working
on the product tests using devices that imitate actual cars in Technology
Section 4.
DENSO is expanding as a global automotive component manufacturer, currently having about 200 group companies in 38 countries in the world in addition to its domestic bases, with about 150,000 employees altogether.
|
|
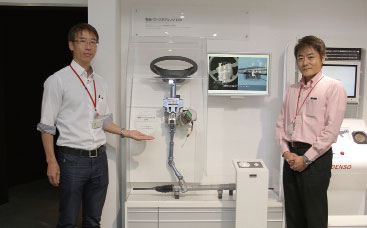 |
"2-Drive EPS" exhibited in DENSO Gallery |
|
Developed 2-Drive EPS to Clear Hurdles by Making the Best Use of Advantages of EPS
Mr. Nakane begins by saying, "The basic EPS system contains steps from operating the steering wheel to moving the tires." According to him, the mission of Electronic Control Components Division includes three elements: 1) Based on signals such as of a torque sensor, 2) ECU (Electronic Control Unit) calculates the optimum motor output (assist force), and 3) Drives the motor based on the command value from ECU.
In the latter half of the 1980's, since EPS was mounted for the first time in light vehicles with small engine output (Kei car), EPS has been replacing hydraulic power steering that was the mainstream gradually. Since oil pressure is generated using engine output, it is always generated while turning on the engine. It takes piping space as well as produces waste oil. In contrast, EPS is excellent in mountability and contributes to improvement in fuel efficiency since it assists electrically only when needed. It also has an advantage of operating a wheel lightly during engine stop. These have made EPS spread rapidly since about 2000.
Just as similar to the other electric products mounted in the vehicle, EPS is composed of a large number of electronic components. Though very rare, the likelihood that a problem occurs is not zero. Moreover, if there is anything unusual to power steering, it may happen that the steering wheel rapidly becomes hard to turn sharply, leading to a traffic accident. Therefore, it has been urged to take some sort of countermeasures. It is the above-mentioned 2-Drive EPS that DENSO developed as its solution for the first time in the world. This has 2 independent drives of the electronic circuit and coil of the motor. The assist force is divided into them to support each other. If a fault should occur to one of the drives, the other drive instantly continues to assist the function of turning a corner. It is so designed to maintain traveling that is safe, secure, and smooth.
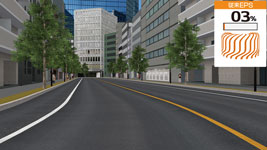 |
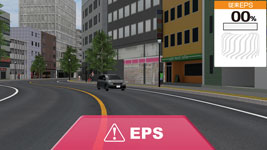 |
1. Traveling in an urban area with a traditional
EPS (driving smoothly with light steering wheel) |
2. A problem occurs with traditional EPS
(hard to drive with heavy wheel) |
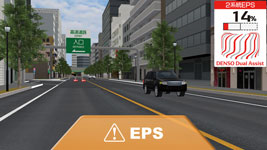 |
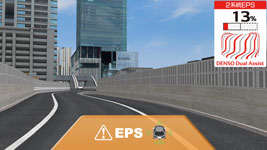 |
3. A problem occurs with 2-Drive EPS (driving
just as usual with light wheel) |
4. A problem occurs with 2-Drive EPS during
automated driving
(capable of maintaining automated driving) |
VR images of the EPS drive simulator: appealing the product value of 2-Drive
EPS using bodily
sensation of a series of simulation scenes |
Process of Developing DS Capable of Bodily Sensing the Effect of 2-Drive EPS
"No matter how much we say in words that (a vehicle mounting 2-Drive EPS) will be safe, it is hard to communicate the pleasure (brought about by that) (to other people) without actually experiencing it."
Though they commercialized 2-Drive EPS in advance, partly because their
competitors seemed to follow them, they wanted to have its advantages to
be recognized early on widely. In addition, as for EPS, they also wanted
to release the restrictions due to its business form of "Tier 2"
(subcontractors) to improve a degree of recognition of the user about their
technological capacity. Especially, when a problem occurs with general
EPS, it might be possible to understand theoretically that steering becomes
heavy, but it is hard to imagine how much and what kind of influence it
has on driving. In searching for effective solutions for such needs and
problems, they thought that the best way was to allow people to experience
it by themselves. However, using actual cars was risky, and consequently
the place and number of people for the test drive had to be limited. Thus,
in order to allow as many as people to experience 2-Drive EPS, they hit
upon development of EPS Drive Simulator (DS), says Mr. Arimoto.
In 2013, using UC-win/Road that was used in other section within the company
for other purpose, they represented a simple zigzag road with VR by themselves.
Disassembling commercial game machines to utilize the parts, they linked
the steering wheel mechanism (hardware) with feel close to an actual car
with VR data. Having test subjects to drive it, they built up an object
that enabled the driver to bodily feel what would happen if there should
be any fault to 2-Drive EPS. In their private booth installed at "Tokyo
Motor Show 2013" in that year, they had the DS tried by their customers
who had business relations with them. It was favorably evaluated more than
expected.
Following this, the next year, in 2014, they introduced UC-win/Road on
a full scale. Mr. Arimoto and others prepared a scenario, and created VR
data for the scene of traveling along an actual townscape. By linking the
accelerator, brake, control operation of EPS and so on with cables and
operating it "while exchanging data in an analogue way," (by
Mr. Arimoto), they produced DS in-house, which enabled bodily feeling to
tell the difference between usual EPS and 2-Drive EPS when a problem occurs.
It was used in new product exhibition within the Company and so on.
Since 2015, they introduced CAN (Controller Area Network), changing the form to that of exchanging different kinds of data on the sides of UC-win/Road and DS. As a result, the development period was shortened and specification change became easier. Moreover, linking diverse information caused variations of simulation to expand. In addition, in the same year, mass-production of 2-Drive EPS started. It became possible to open DS to public on the center stage. The DS was exhibited in the motor shows held at Tokyo as well as Frankfurt, German. Along with this, a version with English guidance for international events was created, in which the car travel on the right lane along townscapes of Europe and United States of America.
|
Since then, they upgraded the VR version every year with Mr. Amakusa as the core person by trial and error as to what kind of scenario could allow the user to easily understand it. In 2016, they prepared a scenario on the assumption that some faults should occur to EPS while traveling on an expressway by automated driving. Its outcome was made open to public in The World Congress on Intelligent Transport Systems 2016 Melbourne.
Further this year, they created VR by mixing the scenes of traveling on general roads in urban areas and on expressways. The DS mounting the latest version was exhibited in the Automotive Engineering Exposition in Yokohama (in May) and Nagoya (in June).
|
|
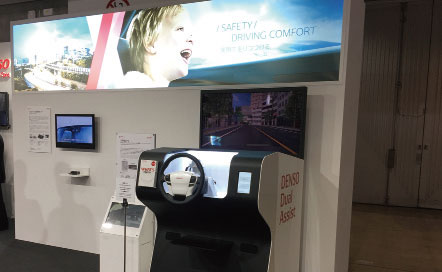 |
EPS Drive simulator exhibited in an exhibition |
|
Evaluation on EPS DS, and Expectation Towards New Possibilities
"The manufactures of B to B (business-to-business), we have few opportunities of hearing real voices of end users." However, by obtaining direct reaction from the test subjects who experienced bodily sensations of the DS, the motivation of the concerned people should get higher, leading to quality improvement. In addition, since Mr. Nakane had been posted overseas until last year and took the guiding role in the Frankfurt Motor Show 2015, he thought that the DS should not only be understood by general users with ease but also give an impact on their domestic and international competitors.
Mr. Amakusa, who saw the images created with UC-win/Road for the first time in the 2014 version of their DS, remembers that his first impression was like "how amazing the screen images are!" Since then, images made progressions every year along with version upgrades. Relative to its backdrop, he mentions the full support by FORUM8, with the viewpoint of him working on producing the DS since 2016.
On the other hand, partly because there are some restrictions to using actual vehicles only for the test in the process of assessing the products, they are examining a shift to assessment using simulation. To realize this, it is critical for the DS itself to realize reality in various terms more highly. Mr. Arimoto expects new possibilities for utilizing the DS in the product assessment process in the future, in consideration of response to automated driving and advanced driving support, connected cars, electric vehicles etc., which are hot topics in the automotive product area.
|